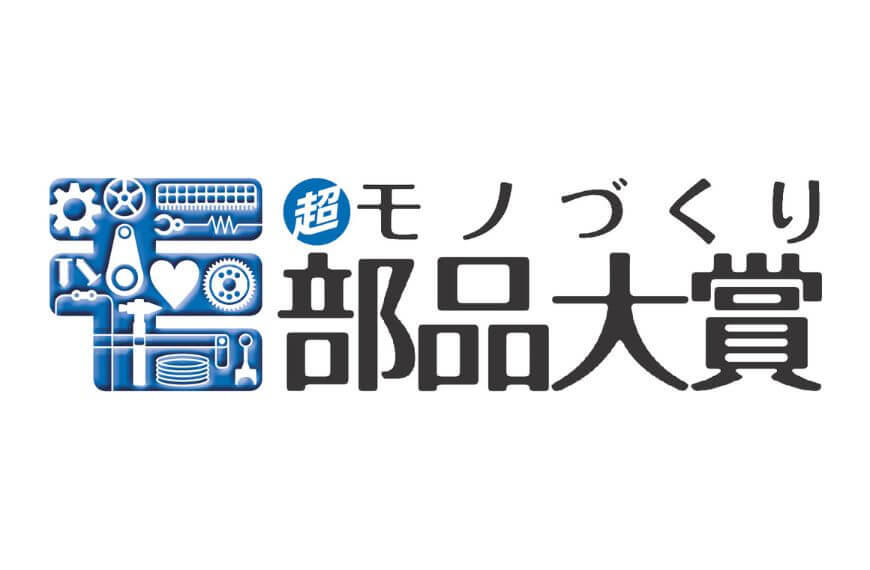
This time, our "PTFE diaphragm" won the "Mobility-related Parts Award" at the 21st Cho Monozukuri Parts Awards. This "PTFE diaphragm" is installed in the Small Lunar Landing Demonstration Vehicle (SLIM), which made the world's first pinpoint landing on the moon.
What is the Super Monodzukuri Parts Award?
The Super Monodzukuri Parts Awards is sponsored by the Monodzukuri Nippon Conference and The Nikkan Kogyo Shimbun, and is awarded to outstanding parts and components that contribute to Japanese manufacturing in six fields: "Machinery and Robots," "Electricity and Electronics," "Mobility-related," "Environment, Resources and Energy-related," "Health and Welfare, Bio and Medical Equipment," and "Solutions to Life and Social Issues." The judging committee, consisting of The Nikkan Kogyo Shimbun and the NPO Monodzukuri Life and Civilization Organization, is a screening committee that widely solicits, judges and awards outstanding parts and components that contribute to Japanese manufacturing in six fields: "Machinery and Robots," "Electricity and Electronics," "Mobility-related," "Environment, Resources and Energy-related," "Health and Welfare, Bio and Medical Equipment," and "Solutions to Life and Social Issues."
What is the fluoroplastic product "diaphragm"?
fluoroplastic product "diaphragm" is an elastic "membrane" that separates the mechanical parts of the pump from the liquid being pumped. Generally, diaphragms are made of metal or rubber, but the diaphragm we manufactured this time is a very large product made of 100% fluoroplastic (PTFE) with a diameter of 830 mm, height of 160 mm, thickness of 0.6 mm, and a mass of approximately 4.0 kg. The thickness varies from area to area, and it was manufactured using high-precision cutting technology.
We can cut different thicknesses, so if you are interested, please feel free to contact us.
In what part of "SLIM" was it used?
Our diaphragms are used in the oxidizer storage section of the fuel and oxidizer storage tank, which is the main structure of the lunar probe "SLIM." "SLIM" will be placed into lunar orbit and will perform reverse thrust to burn fuel during orbit adjustments and lunar landing, but thrust requires the diaphragm to be dented. Conventionally, the diaphragm was made of titanium, but there were issues with metal, such as the stiffness and weight of the denting movement. For this reason, fluororesin was selected fluoroplastic is less susceptible to changes when in contact with oxidizer, and is lighter and softer than metal.
Unlike general-purpose resins, fluoroplastic is a high-performance plastic that combines various characteristics such as chemical resistance, heat resistance, Weatherability, and lowest friction. Other fluoroplastic products manufactured by our company are also used in the engine sliding components of JAXA's H2 and H3 rockets, taking advantage of their "lowest friction" characteristic.
* Reference material for tank interior schematic: JAXA "SLIM Project Overview"
<Diaphragm in a concave state>
How was the fluoroplastic product "Diaphragm" developed?
In 2014, the Japan Aerospace Exploration Agency (JAXA) directly contacted us to ask about developing a fluoroplastic diaphragm for the "SLIM" probe, and development began.
During the development process, we encountered an issue of difficulty in processing fluoroplastic thinly. In order to reduce the weight of the diaphragm, it is necessary to thin fluoroplastic (reducing its thickness). As fluoroplastic is a resin that easily deforms, it is difficult to perform high-precision cutting processing. In addition, changes in thickness affect the movement of the diaphragm, so we had a hard time achieving the required movement and processing precision.
However, by applying the processing technology we have cultivated thus far and devising a fixing method during processing, we succeeded in thinning the tank to less than 1 mm.In addition, because the development center of Mitsubishi Heavy Industries, which develops the tank body to which the diaphragm is attached, is also located in Nagasaki Prefecture, we were able to quickly repeat testing and prototyping, which led to the completion of the product.
lastly…
Up until now, our company has taken on the challenge of processing fluoroplastic in various ways. In the future, we will strive to meet the needs of our customers in a wider range of fields than ever before. We would like to continue to support the lives of many people behind the scenes, leveraging our strengths of top-level technical capabilities that we have cultivated over the years and our corporate attitude of trying to create new things to solve our customers' problems.